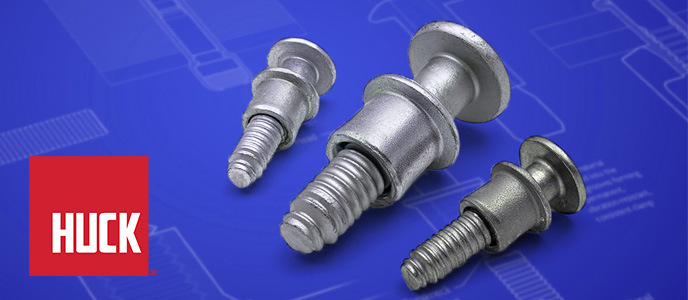
Let's dive into the world of HUCK fasteners and explore how they are reshaping the industrial and transport sectors. Ovesco, your trusted source for all things HUCK, is proud to present an in-depth look at these exceptional fastening solutions.
When it comes to securing components with unwavering strength and durability, the choice between HUCK fasteners and traditional welding becomes clear. Embrace five key advantages that set HUCK apart: unparalleled vibration resistance, superiority over torque, time efficiency, weight reduction capabilities, and a commendable ability to combat corrosion.
1. HUCK Resists Vibration: A Steadfast Solution
In the realm of vibration resistance, HUCK fasteners reign supreme. Fusing precision engineering and advanced joining technology, HUCK equips you with an unparalleled advantage against the relentless forces of vibration, ensuring steadfastness in even the most challenging conditions.
2. HUCK Outperforms Torque: Elevating Standards
In the realm of clamping and torque, HUCK fasteners stand tall, offering precise installation that guarantees a consistent and robust clamp force. Say goodbye to the uncertainty that often accompanies conventional torque methods, as HUCK ensures reliable, certified maintenance-free joints.
3. HUCK Saves Time: Enhancing Productivity
The adage "time is of the essence" holds true, and HUCK fasteners seamlessly align with this principle. Elevate your productivity and efficiency through swift assembly, putting an end to protracted processes and welcoming an era of streamlined operations.
4. HUCK Reduces Weight: A Balance of Strength and Lightness
The pursuit of strength need not come at the expense of weight. HUCK fasteners have unlocked the secret to harmonising strength and weight reduction, rendering a compelling solution that encompasses both robustness and vibration resistance.
5. HUCK Combats Corrosion: Introducing HUCKGuard™
Corrosion is a formidable adversary, and HUCK has taken measures to combat this menace. HUCKGuard™ fortifies your fasteners with a superior level of corrosion resistance, providing unwavering performance in the face of harsh environmental factors.
How HUCKBOLTS Work
Now, let us delve into the mechanics of HUCKBOLTS. This two-piece fastening system comprises a hardened metal pin and a swaged metal collar. The collar seamlessly interlocks with the grooves of the pin, generating a precisely measured clamp force that securely holds assembled components together.
The HUCK installation tool grips the pintail of a HUCKBOLT and then pulls to close the gaps in the materials being joined. Within the nose assembly, a hardened-steel, conical-shaped anvil is then forced down the collar to progressively squeeze, or swage, the collar material into the grooves. This direct metal-to-metal contact keeps everything locked tight, eliminating the loosening effects of transverse vibration.
A HUCK tool swages collar material into grooves, reducing diameter and increasing length. This stretches the pin, ensuring a consistent clamp. This process allows HUCKBOLTS to provide greater tensile strength by filling more grooves than traditional nuts on bolts of similar size and grade.
Key Features:
- Often installs in Under 2 Seconds
- Consistent, High Clamp Force
- Certified Maintenance-Free Joints
- High Shear, Tensile, and Pin Strength
Additionally, HUCKBOLTS have higher shear strength due to engineered pin grooves, resulting in a wider core diameter compared to traditional bolts. This translates to an unparalleled grip and enhanced reliability for your assemblies.
How HUCK Structural Blind Fasteners Work
HUCK's innovative structural blind fasteners are meticulously designed to tackle a wide array of manufacturing challenges effectively. Whether it's rapid assembly, hole-filling, water resistance, accommodating broad grips, replacing welding, or facilitating applications with one-sided access, our fasteners are crafted to deliver industry-leading solutions.
Installation is a straightforward process across all fastener types, utilising our comprehensive selection of HUCK tooling and nose assemblies.
The process begins as HUCK structural blind fasteners are inserted through aligned holes in the materials to be joined. The tool's nose assembly grips the pintail and pulls the mandrel head towards the sleeve, prompting the sleeve to either expand or form a bulb on the blind side of the hole. Within mere seconds, this action draws the materials together, securely locks the mandrel and sleeve, and cleanly breaks the pintail flush with the rivet head.
Key Features:
- Facilitates One-Sided Access Joins
- Outstanding Gap Pull-Out and Retained Clamp
- Unmatched Shear, Tensile, and Pull-Out Strength
HUCK Structural Blind Rivets ensure a robust lock on the blind side, achieved through sleeve bulbing or expanding. The sleeve, strongly supported by the securely fastened bolt, effectively resists failure along its central axis. The compression of the sleeve forms a sturdy bulb, firmly pressing against the joint material. With the bolt permanently secured, the pintail fractures, successfully completing the installation. Alternatively, by tugging on the pintail, the bolt head retracts into the sleeve, generating a secure footprint that firmly engages with the joint material.
Ovesco proudly stands as your authorised distributor and the sole HUCK-certified repair centre in Australia. Our commitment to excellence, paired with HUCK's pioneering advancements in fastening technology, positions us as your partner of choice in achieving sturdy, dependable, and efficient assemblies.